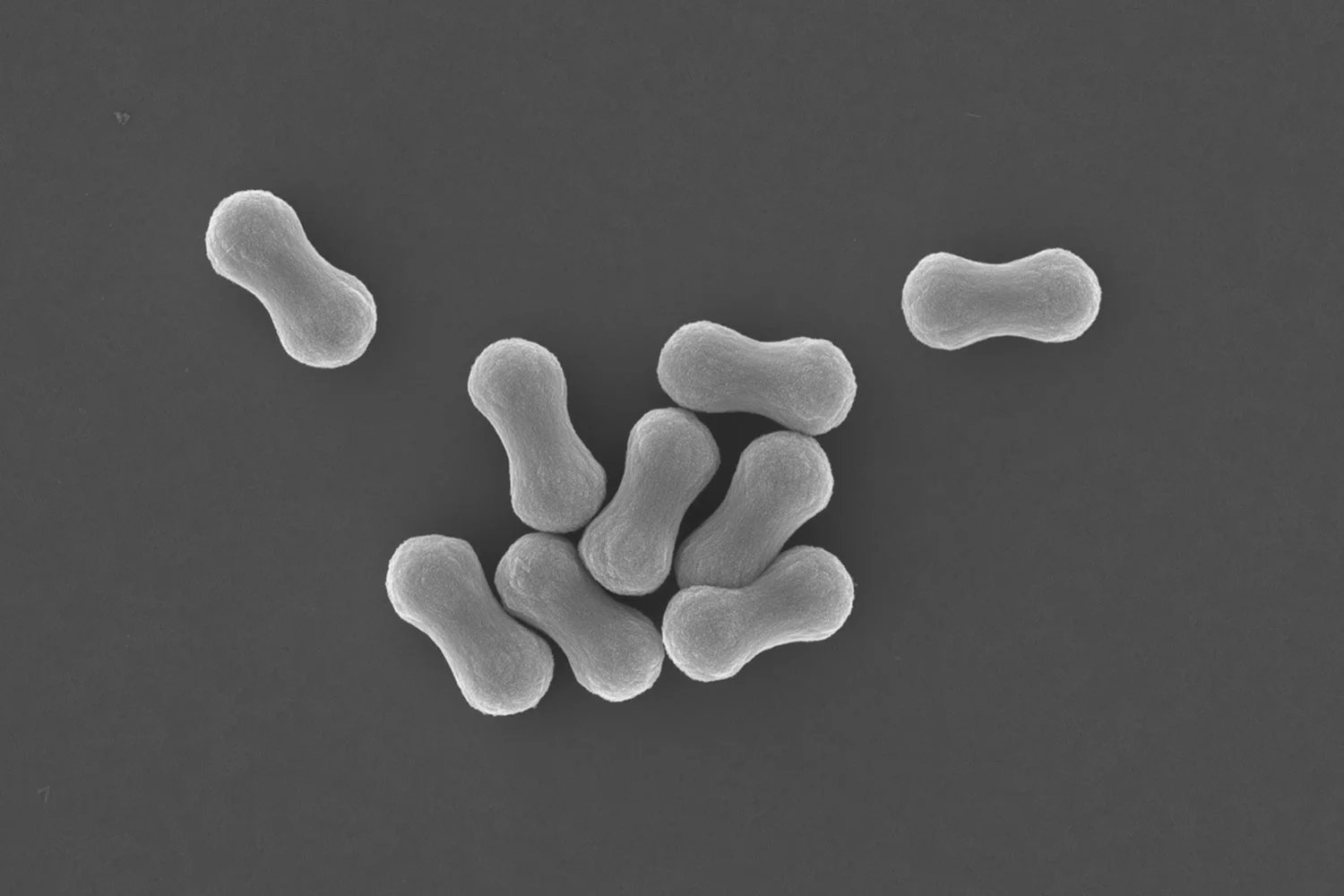
BONLAB BLOG
Thoughts
&
Scientific Fiction
Replacing titanium dioxide as opacifier: consider a shape change
A fresh lick of paint breathes new life into a tired looking place. Ever wondered how a thin layer of paint is so effective in hiding what lies underneath from vision? Beside colour pigments, and a binder that makes it stick, paints contain microscopic particles that are great at scattering light and turning that thin layer of paint opaque. The golden standard for these opacifiers is small titanium dioxide particles, of dimensions considerably smaller than one micron. Their use is not without controversy, as they pose a significant environmental burden, with a substantial carbon footprint and a questionable impact on human health. Ideally, though, titanium dioxide should be replaced, but the list of safe, high refractive materials is very limited. Here we provide a potential solution.
A fresh lick of paint breathes new life into a tired looking place. Ever wondered how a thin layer of paint is so effective in hiding what lies underneath from vision? Beside colour pigments, and a binder that makes it stick, paints contain microscopic particles that are great at scattering light and turning that thin layer of paint opaque. The golden standard for these opacifiers are small titanium dioxide particles, of dimensions considerably smaller than one micron. Their use is not without controversy, as they are a big environmental burden, with a large carbon footprint and a questionable impact on human health. The reason why titanium dioxide particles are great at scattering light is that they have a high refractive index compared to the other paint ingredients, so when distributed throughout the dried paint film their hiding power of the underlying surface is fantastic. When no coloured pigments are used, the coated surface appears then whiter than white.
Ideally though, titanium dioxide should be replaced, but the list of safe high refractive materials is very limited. This makes you wonder if there is another handle, beside refractive index? Can we design efficient scattering enhancers from materials of lower refractive index?. Inspiration came from the white Cyphochilus beetle, native to southeast Asia. The scales of the beetle are not made of high refractive index materials, but they thank their white appearance to an intricate anisotropic porous microstructure, resembling the bare branches of a dense bush.
We at BonLab formed a team where researchers dr. Brooke Longbottom and dr. Chris Parkins together with dr. Gianni Jacucci and prof. Silvia Vignolini at the University of Cambridge (UK) designed a simplified mimic in the form of tiny rodlike silica particles and compared their scattering performance with spherical silica particles.
Our work published in the Journal of Materials Chemistry C from the Royal Society of Chemistry is part of their HOT paper collection and shows that the anisotropic silica particle outperform their spherical counterparts, and show excellent scattering performances across the visible electromagnetic spectrum when casted as a film.
SEM images and optical characterization of white silica supraparticles. a) low magnification SEM image of supracolloidal balls, b) higher magnification image of single supracolloidal balls, c) supracolloidal ball assembled in the presence of 0.01 M calcium chloride. Scale bars: a) = 15μm b&c) = 10μm. d) Reflectance spectra comparing the scattering properties of supraparticles with films of silica rod particles of similar size (thickness of 25μm). Supraparticles show performance comparable to the corresponding films. Increasing the disorder reduces the scattering efficiency. The reflectance spectra for the supraparticles were measured using a microscope, while for the film they were retrieved from the total transmission data.
We did not stop there, and went a step further to develop a prototype of a new class of micron-sized hiding pigment. We took these rodlike silica particles and assembled and sintered them into stable porous supracolloidal microspheres, as can be seen in the image above.
Prof. dr. ir. Stefan Bon says: “This work has been a number of years in the making. It was an absolute pleasure to work with prof. Silvia Vignolini and her team. We are very happy with the end result. We hope that this new type of hiding pigment provides inspiration to those who wish to replace titanium dioxide. After all, there is more to opacifiers than refractive index.”
The paper can be accessed from here:
https://doi.org/10.1039/D1TC00072A
BonLab fabricates textured microcapsules through crystallization
Watch the Talk by clicking here.
Microcapsules can be found in a range of commercial applications, including cosmetics, healthcare, agriculture, and food. The capsules serve as a storage vessel for an active ingredient, for example a nutrient or fragrance. They can have a variety of designs, the simplest form being a single internal liquid-based core surrounded by a solid shell. The chemical and physical characteristics of this shell influence the colloidal stability of capsules in formulations, dictate the permeability and mechanical robustness of the capsules, and can potentially regulate substrate adhesion. Beside storage, these features of the microcapsules are there to regulate and control release and delivery of the active compound.
A considerable part of the technologies used to produce microcapsule relies on the use of synthetic polymers that do not break down, with terrible consequences for environmental build up. One way is to make use of biocompatible and degradable plastics.
We provide an alternative solution, in that we fabricate the capsule from small molecular compounds, instead of polymers, that can crystallize.
Microcapsules can be found in a range of commercial applications, including cosmetics, healthcare, agriculture, and food. The capsules serve as a storage vessel for an active ingredient, for example a nutrient or fragrance. They can have a variety of designs, the simplest form being a single internal liquid-based core surrounded by a solid shell. The chemical and physical characteristics of this shell influence the colloidal stability of capsules in formulations, dictate the permeability and mechanical robustness of the capsules, and can potentially regulate substrate adhesion. Beside storage, these features of the microcapsules are there to regulate and control release and delivery of the active compound.
A considerable part of the technologies used to produce microcapsule relies on the use of synthetic polymers that do not break down, with terrible consequences for environmental build up. One way is to make use of biocompatible and degradable plastics.
We provide an alternative solution, in that we fabricate the capsule from small molecular compounds, instead of polymers, that can crystallize.
Artist impression of textured microcapsules made through crystallization.
In our work, published in the scientific journal ACS Applied Materials & Interfaces we focus on the fabrication of microcapsules of which the capsule wall is composed of an inter-locked mesh of needle-like crystals, which besides capsule rigidity and semi-permeability, provides a roughened surface texture.
In this proof-of-concept study crystals of the small organic compound decane-1,10-bis(cyclohexyl carbamate) are formed within the geometric confinement of emulsion droplets, through precipitation from a binary-solvent dispersed phase. This binary mixture consists of a volatile solvent and non-volatile carrier oil. Crystallization is facilitated upon supersaturation due to evaporation of the volatile solvent. We show that the microcapsule diameter can be easily tuned using microfluidics.
The technology is shown to be scalable using conventional mixers, yielding spikey microcapsules with diameters in the range of 10-50 μm. We highlight that the capsule shape can be molded and arrested by jamming using recrystallization in geometric confinement.
With an eye on commercial applications we show that these textured microcapsules show enhanced deposition onto a range of fabric fibers. They outperform their traditional polymeric analogues by sticking better on fibrous substrates.
Prof. dr. ir. Stefan Bon says: “I am delighted with this work, a coordinated effort which was led by first author dr. Sam Wilson-Whitford. A while back we decided in BonLab that our science needed to be greener, and more sustainable. We think our way of making textured microcapsules meets these criteria. We hope that it inspires industry, and that the concept will prove to be useful across a variety of application areas.”
The paper can be accessed here:
https://pubs.acs.org/doi/10.1021/acsami.0c22378
A talk on the topic can be accessed here:
https://www.formulation.org.uk/pc20programme/250-past/2021/pc20/860-pc20-bon.html
What happens to particle size distributions when making reactive surfactants and polymer colloids by emulsion polymerization?
When we synthesize polymer colloids by emulsion polymerization, molecular surfactants are often employed. These are required to keep the polymer latex particles dispersed in the water phase, so that they do not clump together, a phenomenon known as coagulation. Keeping polymer dispersions stable is especially important in end applications, such as waterborne coatings and adhesives.
A downside of the use of surfactant molecules is that they can desorb from the surface of the latex particles. This makes the particles colloidally unstable, and they coagulate. This can be disastrous in product formulations, such as water-based paints which have many components. Another downside of this mobility of the surfactant molecules is that they can migrate in the final coating, once applied on a substrate. This leads to deterioration of the properties of the coated film.
When we synthesize polymer colloids by emulsion polymerization, molecular surfactants are often employed. These are required to keep the polymer latex particles dispersed in the water phase, so that they do not clump together, a phenomenon known as coagulation. Keeping polymer dispersions stable is especially important in end applications, such as waterborne coatings and adhesives.
A downside of the use of surfactant molecules is that they can desorb from the surface of the latex particles. This makes the particles colloidally unstable, and they coagulate. This can be disastrous in product formulations, such as water-based paints which have many components. Another downside of this mobility of the surfactant molecules is that they can migrate in the final coating, once applied on a substrate. This leads to deterioration of the properties of the coated film.
A solution to these problems is to use reactive surfactants. These have the ability to attach themselves to the latex particles irreversibly, through a covalent chemical bond.
Catalytic chain transfer polymerization (CCTP), a free radical polymerization processs that employs a cobalt catalyst in tiny amounts, is able to make polymer molecules with a reactive unsaturated end group. These macromolecules, also called macromonomers, can be chain extended using a process referred to as RAFT (Reversible Addition Fragmentation chain Transfer), into longer polymer molecules that can behave like surfactant molecules. The reactive end group is preserved, which means that if our polymer reactive surfactant is used in an emulsion polymerization to make latex particles, it will be attached permanently to the latex particles.
The technology to fabricate blockcopolymers under emulsion polymerization conditions using CCTP derived macromonomers, was originally reported in the 1990s by Moad and coworkers. Emphasis has been lying on polymer chain growth and hence the molecular weight distribution.
In our paper published in a special polymer colloids issue of the ACS journal Biomacromolecules PhD students Wai Hin Lee and Joshua Booth investigated the emulsion polymerization processes from a different angle. We investigated the particle size distributions and studied how these developed throughout a three-stage emulsion polymerization process (see the image below).
Three stages of emulsion polymerizations: Catalytic chain transfer emulsion polymerization to make an alkali soluble macromonomer, chain extension to make a reactive block copolymer surfactant, emulsion polymerization to prepare soft polymer colloids using the reactive surfactant.
Firstly, we looked at the catalytic chain transfer emulsion polymerization to make the hydrophilic block of the reactive polymer surfactants. Next we looked at how the particle size distributions changed upon chain extension with a hydrophobic block. Finally, we disintegrated the latex particles into a reactive polymer surfactant micellar dispersion. This was then used to carry out emulsion polymerizations to produce polymer latexes in absence of conventional surfactants.
Prof. dr. ir. Stefan Bon says: “I hope that people like the angle we took in our work, to shine a light on how the latex particles are formed and how the particle size distributions develop. We showed that it was possible to make soft polymer latexes with average particle diameters below 100 nm using our reactive surfactants, easily up to overall solids content of 30wt%. This is an excellent achievement. We believe that the reported emulsion polymerization processes are robust and versatile, and are delighted that we can produce polymer latexes that do not suffer from surfactant migration upon application.”
Details on the paper : https://pubs.acs.org/doi/10.1021/acs.biomac.0c00766